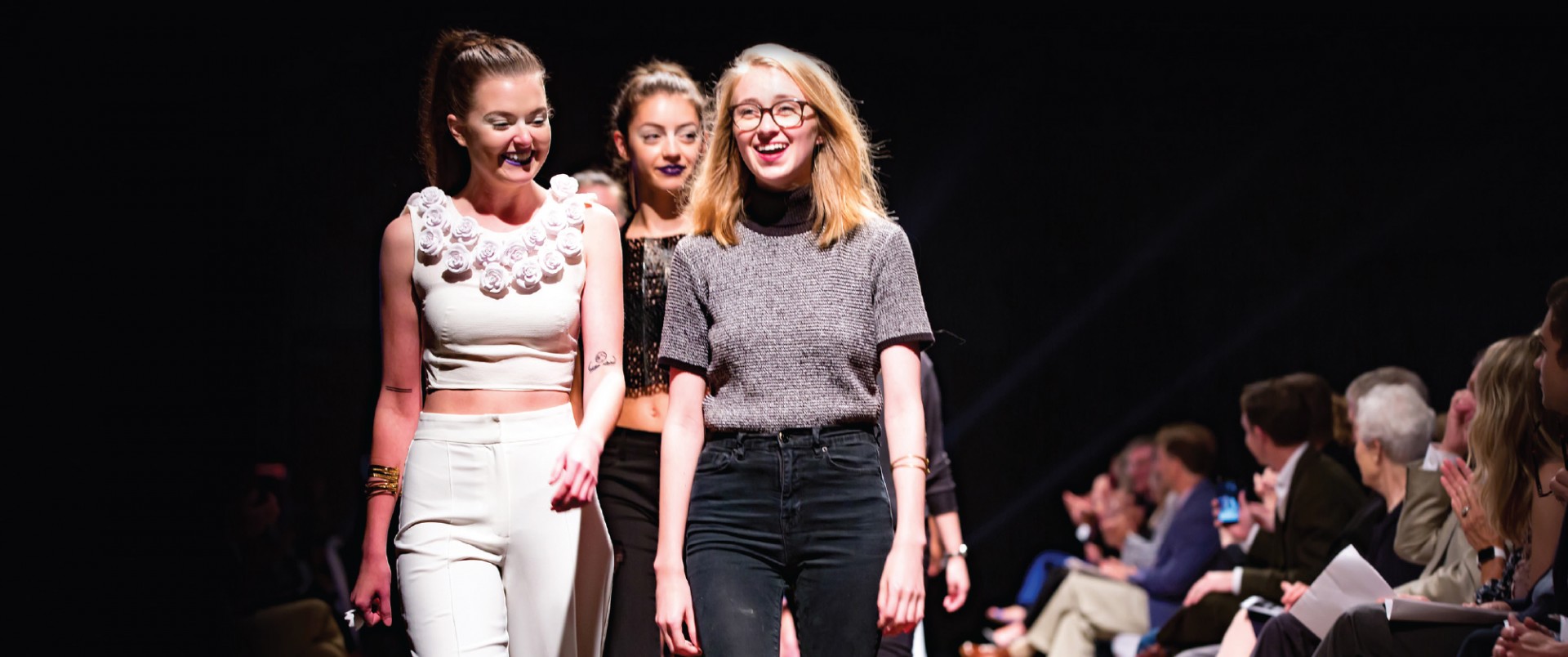
Fashion for the 21st-Century Flower Child
“They’re incredible! Katie and Laura took a dream I had and made it happen – they’ve opening up a whole new area of research for our program.”
The theme was “Futuristic Floral” and the student designers rose to the challenge: the models who strutted down the runways were illuminated, caged, chained, caped and swathed in yards of tulle, silk, spandex, lace and vinyl. Within this extravaganza of flowered fancy dress, a simple black crop top with a punched rose motif stood out as something you might actually wear.
That crop top, designed and fabricated by honors students Laura Corral and Katie Walker for their honors thesis, might just be the most revolutionary piece in the end-of-year fashion show, which was hosted by the Apparel Merchandising and Product Development program in the School of Human Environmental Sciences. That’s because Corral and Walker printed the crop top on a 3D printer, using thermoplastic urethane (TPU) to achieve a fluidity similar to leather or fabric.

Laura Corral and Katie Walker assemble the crop top
“They accomplished a fantastic feat in a short amount of time,” said Joshua Van Vleet, director of operations of NWA 3D, which sold the equipment to the university. Van Vleet provided technical assistance to Corral and Walker throughout the production process. “Working with TPU – imagine trying to push a rope up hill. Most 3-D material is rigid and printed with joints. These students have opened up all kinds of possibilities that the industry is avoiding right now, because it’s difficult.”
Haute couture designs by Iris van Herpen and Francis Bitonti inspired Corral and Walker to tackle 3D printing, but they put their own spin on it. “During our lit review, we saw what’s been done – really crazy things, very avant-garde,” Katie Walker said. “We decided to produce fashion that you could wear every day.”
Their work began last fall with grant applications to purchase the equipment needed. Thanks to funding awarded by Bumpers College and the Honors College, the printers were purchased, but shipment on, quite literally, a “slow boat from China” delayed their production start date until January.
“We had a huge learning curve with the prototyping process,” Laura Corral said ruefully. “We used online freeware – 123D Design, meant mostly for children – and started building tiles.” After experimenting with a crisscross pattern that failed their strength test, they developed a floral motif that could be repeated and printed into a sheet of material, or tile.
In theory, at least.
“The printers malfunctioned in every way possible!” Corral said. “Printing with the TPU filament is tough – it’s stretchy, and would get stuck in the extruder.” They experimented with different colors and slower feed and flow rates, but at the end of the day, the fact that each 12” by 12” tile took 14 hours to print “really ate up our time,” Walker said.
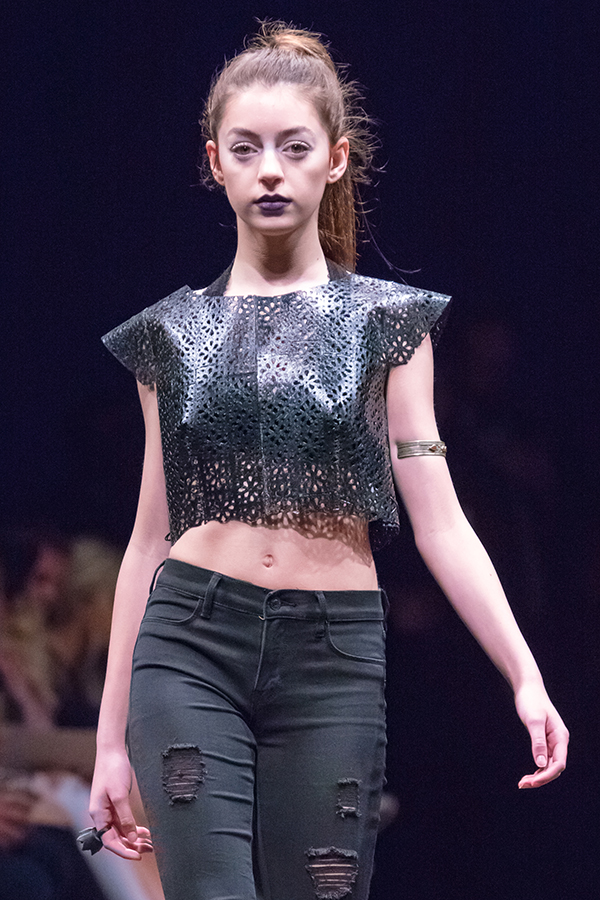
Photo: Russell Cothren
The team received a morale boost when they traveled to San Francisco to attend the Gerber Technology Road Show, which explored new technologies in the fashion industry. There, Corral and Walker connected with Israeli designer Danit Peleg, who designs exclusively with 3D printing, and showed her samples of their tiles.
“We learned that she used glue to put together garments – that validated our production process,” Walker said. They also learned that Peleg uses additive manufacturing, printing just the material needed for a design, rather than the traditional subtractive technique, where patterns are cut from material. “Sustainability and waste are a big issue in the industry,” Corral said. “Our big vision would be to scan clients for their exact measurements, model the garment on a computer, and then they could print it at home.”
Corral and Walker wrapped up work on their honors thesis by conducting surveys in the Arkansas Union and in an introductory class in apparel design. The survey assessed prior exposure to 3D printing, general fashion interest and consumer response to the garment. Overall feedback was positive, with some students saying the top looked like leather, and many expressing interest in further use of 3D printing in the fashion industry.
Perhaps their best review came from faculty mentor Stephanie Hubert, an instructor in the Apparel Merchandising and Product Development program. “They’re incredible! Katie and Laura took a dream I had and made it happen – they’ve opening up a whole new area of research for our program.”
More Field Notes Stories
Capitalizing on Viral Videos
“There are a lot of YouTubers out there who are popular and using products spontaneously, which I believe is more powerful with Millennials.” Six students enter the Walton College Behavioral Business Research Lab, painted a soothing peach color to put them...
Pyramid Power
Garret Gardenhire, Kevin Le and Matt Annis monitor their solar-powered food dehydrator, designed to combat food insecurity in developing countries. Freshmen honors engineering students Garret Gardenhire, Kevin Le and Matt Annis inherited a simple machine and a big...
Growing Up and Growing Old: Developing Research Skills in the Aging Lab
Allen straps on a knee brace, designed to mimic the effects of arthritis on the joints; she hopes that her research will lead to a greater awareness of ageist attitudes.by Samantha Kirby “What?” I asked. “What?” My hearing was poor. I turned toward the speaker, but...
Double Duty for Future MD
As part of his biochemistry thesis, Will Pohlman developed a dye technique that may prove useful to pharmacological companies. Biochemistry and animal science proved to be the perfect double major for Sturgis Fellow Will Pohlman, who dreamed about a career...
Big Picture Data
“Hannah has painted something that everyone can respond to on a personal level, that offers people a way into a place to see it differently.” Rain or shine, at 7 a.m. every Tuesday for five months honors landscape architecture major Hannah Moll showed up, camera in...